Mainter Blog
Optimize Daily Maintenance Management in Your Facility
- Mainter
-
- 5 min reading
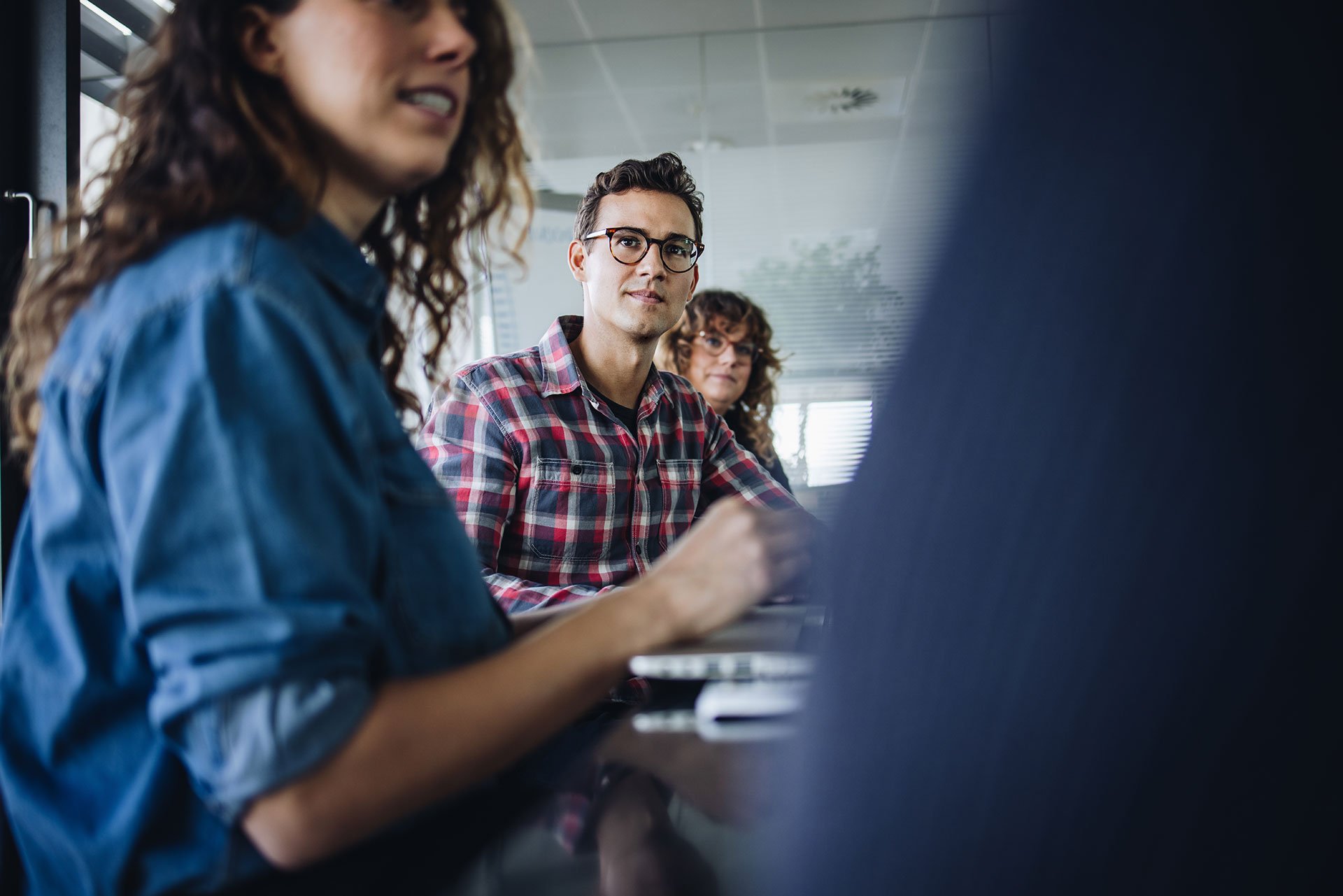
Setra has been using Mainter’s maintenance system for almost a year, and they’ve quickly seen significant improvements. With better planning and smoother workflows, their maintenance department has made great strides forward.
In three articles, we share Setra's insights from the journey with Mainter. This particular one is about how you can use Mainter to streamline your own daily management of maintenance. If you want to take part in the other articles, register for our newsletter.
Setra, one of Sweden’s leading wood industry companies, is known for its sustainable and innovative work, ranging from construction timber to glued laminated products. With the philosophy of “Green Profitability,” they actively contribute to a circular economy and more environmentally friendly construction practices. In this article, Anders Toresson, Setra’s Maintenance Manager in Färila, and Maintenance Planner Patrik Carlström, share their experiences with Mainter’s system and how it has helped improve and streamline Setra’s daily maintenance operations.
A Catalyst for New Workflows
When Setra decided to implement Mainter in October, their goal was clear: they needed to modernize and structure their maintenance processes to maximize efficiency. Their previous system had served its purpose but lacked the flexibility and user-friendliness required for today’s maintenance needs.
Mainter made the transition smooth by simplifying the migration of equipment data and tailoring the system to Setra’s specific requirements. This marked the beginning of a shift in their workflows. Patrik describes the transformation:
“Switching to Mainter was definitely a commitment, but the system’s intuitive design allowed us to get up and running quickly. We also took the opportunity to improve some workflows, which gave us a strong start.”
With Mainter, Setra gained not just a system but also a catalyst for a new, more efficient way of working.
Thoughtful Implementation to Maintain Momentum
Implementing a new maintenance system can often feel overwhelming, but Setra found the transition to Mainter smoother than expected. With a structured and phased training plan, they were up and running within just eight weeks. Patrik emphasizes the importance of a step-by-step approach:
“We conducted phased training, allowing everyone to learn at their own pace. This gave us the chance to ensure everyone was comfortable with the system and that change management was in place.”
Having an implementation plan that supports everyone creates sustainable change, saves time and resources in the long run, and ensures the system’s long-term effectiveness. While there’s always a learning curve, the effort is well worth it.
Measurable Results Driving Improvements
Mainter has enabled Setra to see tangible and measurable improvements in maintenance efficiency. Previously, gaining an overview was challenging, and many maintenance activities went undocumented, making it hard to evaluate what worked and what needed adjustment.
With Mainter, Setra now has clear visibility into work orders and outcomes, helping them make more informed decisions and reduce the number of “black jobs.” Patrik explains:
“Mainter hasn’t just simplified our documentation; it has also helped us work more proactively. We now see exactly what has been done, which tasks require additional resources, and where we can improve our planning moving forward.”
By tracking and analyzing their work, Setra can now set goals and adjust processes based on real data, providing a solid foundation for continuous improvement.
Daily Workflow Structure
With Mainter, Setra has introduced a clearer structure to their daily maintenance work. Previously, work orders were selected randomly, and tasks were often prioritized based on who could make their voice heard rather than actual needs. Mainter has now made it possible to establish a fixed prioritization structure, where daily plans and the planning calendar guide work and ensure each task is handled appropriately.
The maintenance team starts each day with a team check-in (an internal “pulse meeting”) where they review the day’s tasks and priorities. This approach gives the team full control over the workflow and allows them to quickly adjust when changes are needed, boosting both transparency and productivity. Patrik explains:
“We use Mainter’s planning calendar as our hub. Everyone knows what needs to be done and who is responsible for what. We meet every morning to review today’s and tomorrow’s work.”
Pulse Meetings - the foundation of an agile process
After the internal check-in, a facility-wide pulse meeting takes place, bringing together both the maintenance and production teams to coordinate efforts. During this meeting, they review the previous day’s tasks, make necessary adjustments for the following day, and discuss potential challenges, such as missing spare parts. They also jointly assess new needs and prioritize them within the overall task catalog.
If a new task needs to take priority, the team agrees on which other tasks can be postponed. Anders describes the impact on maintenance:
“These pulse meetings are indispensable. They allow us to quickly adapt and get everyone on the same page.”
With Mainter’s features, the meetings have become both visually and structurally clearer, significantly improving communication and creating a workflow where maintenance operations are perfectly aligned with production needs.
Delegation and Independent Responsibility
Setra has introduced daily plans to provide mechanics and electricians with a clear order of priorities. Each team member now has a list of work orders with high, medium, and low-priority tasks, enabling them to handle urgent issues seamlessly. If an urgent task arises, they can easily pause a low-priority task and document the reason in the system.
Mainter allows Setra to delegate responsibility to technicians in a structured way. Technicians know that if a task cannot be completed, they can indicate the reason, making it visible to the entire team during the morning pulse meeting. This setup gives every team member confidence to prioritize based on the day’s actual needs.
“We want to avoid over-administration. That’s why we give technicians the freedom to make their own decisions as long as they prioritize correctly. It reduces our burden and makes the work flow better,” says Patrik.
Communication and Documentation in One Place
Setra has also transformed how they handle communication in the maintenance process. Instead of relying on emails or paper notes, their team can now tag colleagues and leave comments directly on work orders in Mainter. The result? Clearer and faster communication, where everyone stays informed about ongoing and upcoming tasks.
“Being able to @-tag colleagues in work orders means we don’t have to chase each other for information. It’s easier to track who is doing what and when. The system has also minimized misunderstandings since everyone can see the latest status of tasks,” says Anders.
Be Prepared to Invest Time and Resources
If you’re considering optimizing your daily maintenance, Setra advises being prepared to invest time and resources to succeed. It’s not just about switching systems but also about adapting workflows and creating a culture where everyone feels involved.
Anders emphasizes the importance of allowing employees time to adjust to new workflows:
“People learn at different paces. Make sure to support and help them, and don’t be afraid to let the process take time. It pays off in the long run when the entire team starts following it fully. Once everything is in place, the results speak for themselves.”
How to Take Control of Your Daily Maintenance – Practical Tips from Setra’s Journey
Here are some concrete tips from Setra’s experience with Mainter. Use these to strengthen your own daily maintenance management:
- Plan for a Sustainable Implementation
Have a clear implementation plan where everyone gets the support and time they need to adapt. A well-thought-out start helps create a solid foundation for long-term system use. - Introduce Structured Work Planning
Real-time planning allows you to adapt quickly to changes. Mainter’s drag-and-drop functionality makes it easy to adjust work orders and prioritize tasks. - Create a Unified View with Pulse Meetings
Use pulse meetings to ensure everyone is on the same page and can adjust priorities together as needed. With Mainter, you can visualize tasks and reduce meeting time. - Delegate Responsibility with Freedom within Structure
Daily plans allow technicians to manage their own priorities, reducing overload and increasing productivity. Use Mainter to monitor progress in real-time. - Centralize Communication and Documentation
Keep all critical information centralized and accessible to the entire team. With Mainter, everyone has access to the latest information, improving efficiency and decision-making.
Ready to Optimize Your Daily Maintenance? Setra’s journey shows that with the right tools and strategies, you can create both structure and efficiency in your team. Contact us today for tailored tips and solutions designed to meet your goals and needs.