Mainter Blog
How to Create Effective Spare Part Management?
- Mainter
-
- 3 min reading
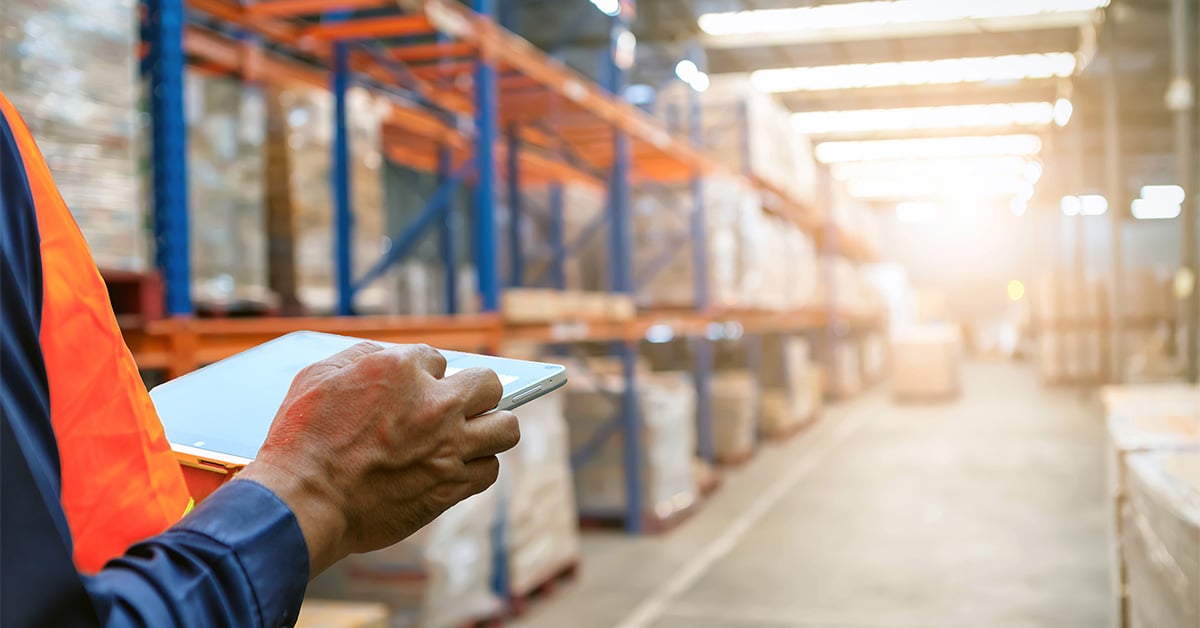
Effective spare part management is crucial for both planned production stops and preventative maintenance. When machines are idle due to a lack of spare parts, it incurs substantial costs, which could often be avoided with effective stock management for maintenance.
Maintenance with Stock Management
It's all about keeping tabs on the spare parts you need to stock, without overspending.
An excessively large stock ties up substantial capital, which could be allocated to other business investments. Moreover, some items risk degrading in quality and surpassing their best-before dates, further emphasising the need for a balanced stock.
Effective spare parts management for maintenance involves:
- Ensuring the business has access to the right spare parts at the right time to replace crucial components.
- Finding the balance and margins regarding which items should always be in stock and which can be procured with a few days' lead time.
- Avoiding emergency stoppages by proactively replacing parts before they fail.
- Establishing procedures so that you can order parts in time, before tasks need to be carried out.
- Maintaining good relationships with suppliers who provide reliable deliveries.
Much to Gain from Effective Stock Management for Maintenance
Many are aware of the benefits of efficient stock management for maintenance.
With effective spare part management and a reliable stock balance. Yet, keeping track of all this is quite challenging with just spreadsheets, paper and pen.
A fundamental requirement for success is thus to use a maintenance system that indicates when machinery should be maintained, providing an overview of stock levels, so that orders can be placed before shelves are empty.
Being able to also get an overview of which spare parts are used for which assets and machines is truly a dream scenario for the entire maintenance department.
So, how does one start and establish this effective stock management for maintenance?
And how does one ensure that essential information about orders and items can be shared among various employees to avoid incorrect orders?
1. Start with the Organisation
No job can be well-executed without knowing who is responsible. Always start with the organisation. Involve those within your company who work with the purchasing and handling of stock management and spare part management. Together, identify how you currently operate, who is responsible for what, and pinpoint the areas where you have deficiencies or face significant time drains.
By prioritising what is most important, a shared understanding is also created. The next step is to clarify the roles to address the gaps you've discovered.
2. Choose a Maintenance System that Supports Spare Part Inventory Management
Then proceed to choose a software support that is both easy to start with and user-friendly so that the organisation adopts it. You'll be living with this maintenance system for an extended period, so the threshold for using it should be low.
3. Take Inventory of All Spare Parts for Machinery
Often, both duplicates and unused items are on the shelves, allowing you to reduce the number of spare parts simply by performing a thorough review. How many of your spare parts are used recurrently and are there parts that can be used for multiple machines?
Also, carry out an appraisal of your stock. This step is considerably easier when you digitise the inventory and can see a summary of everything stored there.
Also, note parts that are extra critical by classifying them. Which spare parts are so important that they should always be stocked, and which are available from the supplier within a few days' lead time? This clarifies how crucial your preventative maintenance intervals are.
4. Establish a Reliable Stock Balance
For everyone to trust the stock balance in the system, collaboration among all parties involved is essential. All staff must log their withdrawals when leaving the storage shelves. The safest approach is to scan spare parts using bar codes or QR codes.
Also, consider deepening your collaboration with selected suppliers. Inquire if they could stock some chosen spare parts at your facility, in a designated area. This could be a win-win situation, as many face challenges related to both space and delivery.
5. Set Goals and See Results
No one can do everything, and not all at once. So, cooperate within the maintenance department and set motivating goals. Also, don't overlook the data generated by a maintenance system. It offers valuable insights into future investments and overall maintenance strategy.
Spare Part Management in the Mainter Maintenance System
With Mainter's spare part management, you get control over your warehouse items, stock balances, suppliers, and purchases. Here, you can manage all your items and easily link them to the appropriate objects or machines. This enables maintenance technicians to follow their work orders and directly see which warehouse items will be needed.
QR Code Labelling
QR codes are an appreciated feature in Mainter, streamlining work orders, facilitating purchases, and reducing the risk of incorrect orders. With QR codes, you can label all your items, which can then easily be scanned with a mobile phone.
This is efficient for both ordering spare parts and for the service technician who can reserve the spare parts that will be needed. Reserved spare parts are flagged in the stock balance, and notifications are sent to warehouse staff for ordering.
A Comprehensive Maintenance System
Mainter is a robust and user-friendly maintenance system with inventory and spare part management, compatible with computers, mobiles, and tablets alike. So, regardless of the device you and your colleagues use, you can access and work within the system.
Here you can also register and manage all your machines and properties. As well as all the preventative and corrective maintenance that you carry out, either in-house or with external maintenance partners.
Finally, the crucial statistics. In Mainter, you set the cost for both internal and external maintenance technicians. Logged working hours and costed spare parts are recorded. Altogether, this provides valuable data that can be easily utilised for both short-term and long-term strategic decisions.